Headquartered in Tigard, just south of Portland, Oregon, Plastic-Metals Technologies/PMT Shielding Solutions is an industry leader in vacuum metallizing principally engaged in the aerospace, defense, and medical industries. Providing EMI/RFI shielding solutions for advanced technology systems in these industries has allowed us to expand our ability to bring you the latest available solutions for your company needs.
Plastic-Metals Technologies is proud of the excellent customer service and on time delivery we bring to your product design and manufacturing teams. In addition to our extensive experience in metallizing, thin-film, and additive coating fields, we offer years of electronics industry product design, operations and manufacturing expertise. We also bring chemical and electronics engineering expertise to your project. You’ll find us a responsive and dedicated partner, and one that can further support your post-metallization needs.
Plastic-Metals Technologies, Inc., provides high-quality thin film metallization services that meet the requirements and expectations of our customers with a focus on continual improvement.
Process
PMT Shielding Process
Vacuum Metallizing vs Traditional Shielding
Vacuum Metallization (Vapor Deposition): Vacuum metallization is a deposition process that enhances electromagnetic interference (EMI) and radio frequency interference (RFI) shielding of products by applying thin metallic layers directly onto housings within a vacuum chamber. This technique allows for precise control over material thickness and composition, enabling the creation of highly effective shielding layers without the need to add additional components. By utilizing multiple metals in a single process cycle, both EMI/RFI reflection and absorption can be optimized. For instance, an initial deposition of copper provides high electrical conductivity and efficient signal reflection, while a subsequent layer of nickel or nichrome improves mechanical durability, corrosion resistance, and enhances absorption of high-frequency interference through its resistive and magnetic properties.
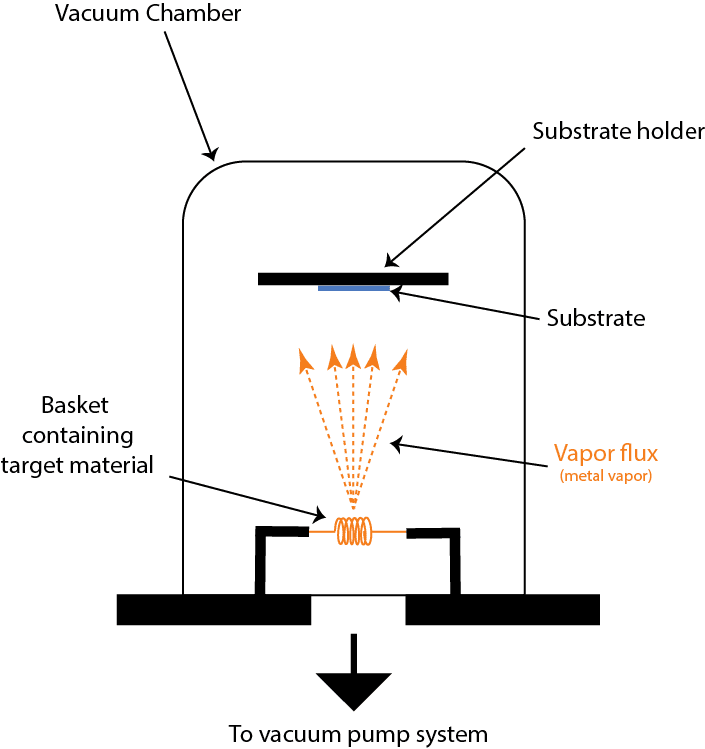
This multilayer deposition approach often eliminates the need for traditional shielding methods such as stamped metal enclosures or conductive spray coatings, which can introduce design constraints and manufacturing inefficiencies. Vacuum metallization allows for uniform coverage on complex geometries, ensuring consistent shielding performance while reducing weight and material usage. Additionally, the ability to integrate shielding directly onto plastic or composite components improves manufacturability by streamlining assembly processes, minimizing production costs, and enhancing overall system performance. The vacuum metallized shielding becomes an integral part of the finished plastic/composite housing. This makes vacuum metallization particularly advantageous for applications in medical devices, automotive, aerospace, and consumer electronics, where efficient EMI/RFI management is critical.
What is EMI & RFI?
RFI (Radio Frequency Interference), which is also known as EMI (Electromagnetic Interference) is any electromagnetic radiation or disturbance which is emitted from an electrical circuit or electronic component that interrupts or interferes with the operation of other electronic components, or electrical circuits. RFI or EMI may be introduced intentionally as in the case of electronic warfare, or unintentionally from an electronic or electrical device or system.
PMT Shielding Solutions uses Physical Vapor Deposition (PVD), which means NO chemicals are involved, only metals from a solid state. The vacuum allows vapor particles to travel directly to the object (substrate), where they condense back to a solid state, thus creating a 1-micron layer consisting of two layers of metal and serving as an extremely dense and high performing EMI/RFI shield.
The two-layer system is what sets PMT Shielding Solutions and Plastic-Metals Technologies apart from any other EMI/RFI shielding company. With proven independent test results, we have found that the combination of Copper and Secondary metal (Aluminum, Nickel) is far superior to a single stage process, and actually provides a more stable, durable, and consistent surface.
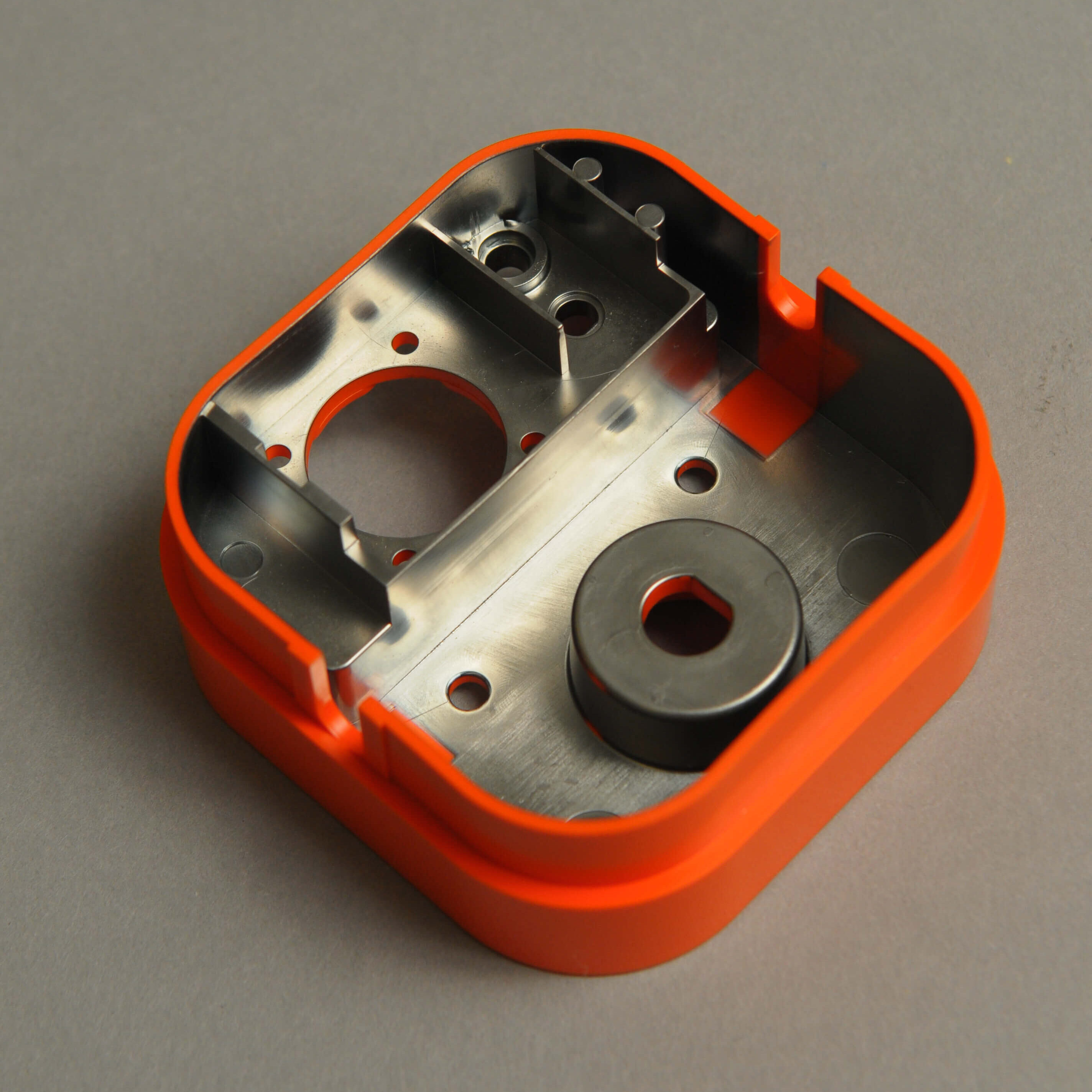