EMI Shielding With Vacuum Metallization – A Two-Layer Approach
The Benefits of Vacuum Metallization for EMI/RFI Shielding: A Two-Layer Approach
In today’s world of high-speed electronics and wireless communication, electromagnetic interference (EMI) and radio frequency interference (RFI) pose significant challenges. Effective shielding solutions are necessary to ensure the optimal performance of sensitive electronic components. One of the most efficient methods for EMI/RFI shielding is vacuum metallization, particularly using a two-layer approach: (1) Nickel over Copper and (2) Aluminum over Copper. This technique provides superior conductivity, durability, and cost-effectiveness when applied to parts made out of plastic, carbon fiber/composites, and other materials.
Understanding Vacuum Metallization for EMI Shielding
Vacuum metallization is a process that deposits thin metal layers onto a substrate using a high-vacuum environment. This method enhances surface conductivity and creates an effective barrier against electromagnetic interference. When applied correctly, vacuum metallization can significantly improve electronic performance by reducing signal degradation and crosstalk. This boost in performance makes it an ideal solution for EMI shielding.
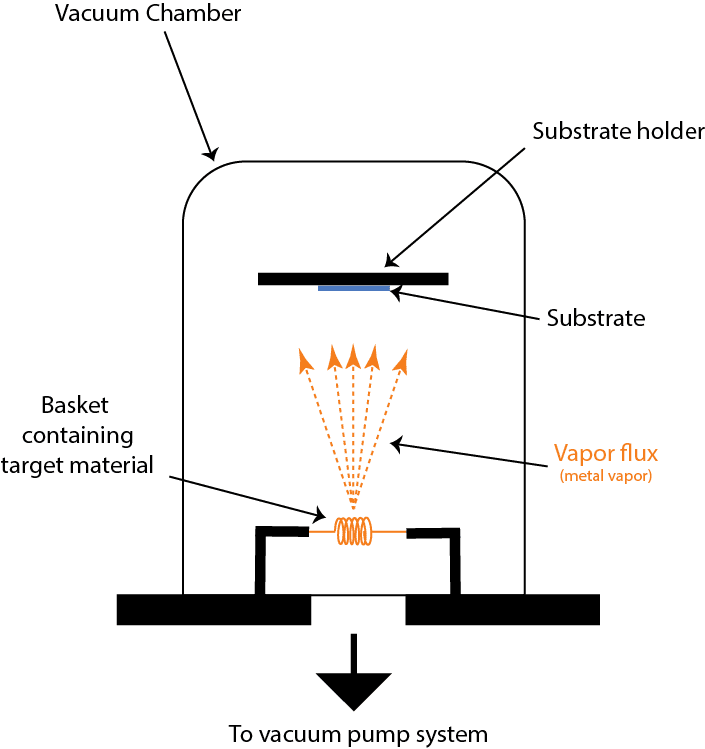
The Two-Layer Approach: Enhancing Performance
1. Nickel Over Copper
Nickel over copper is a widely used shielding combination due to its complementary material properties:
- Copper: Offers excellent electrical conductivity, ensuring efficient dissipation of EMI signals. However, it is prone to oxidation, which can reduce its effectiveness over time.
- Nickel: Acts as a protective barrier against oxidation while also enhancing mechanical durability. It provides a stable, corrosion-resistant surface that maintains the shielding effectiveness of copper over extended periods. This combination is highly effective for EMI shielding applications.
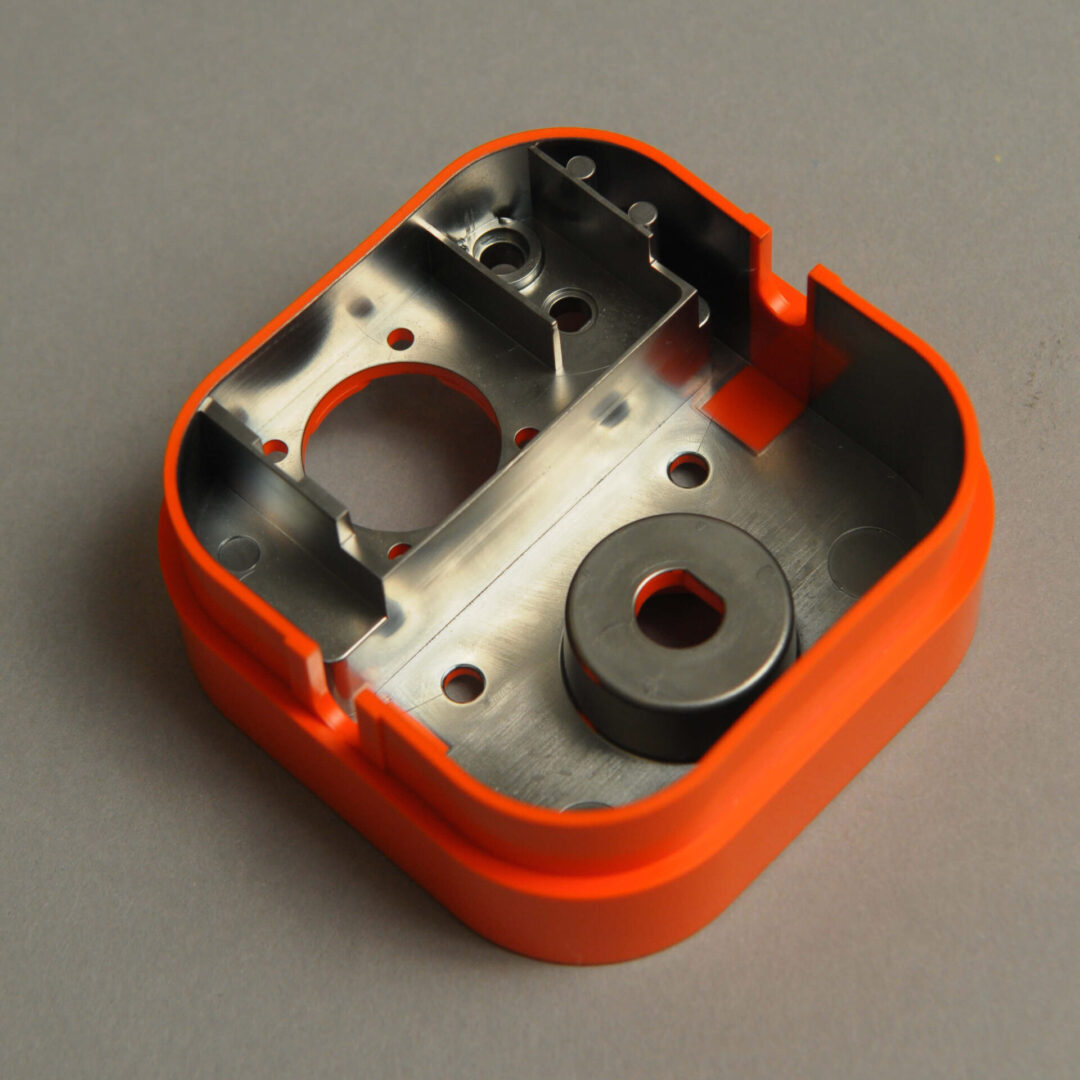
2. Aluminum Over Copper
An alternative to the nickel-copper approach is aluminum over copper, which brings distinct advantages:
- Aluminum: Lightweight, cost-effective, and highly conductive, aluminum is an excellent material for shielding applications. It provides an effective EMI/RFI barrier while adding minimal weight to the final product.
- Copper: Again, serves as the primary conductive layer, ensuring high efficiency in shielding against interference. The combination of these metals results in efficient EMI shielding.
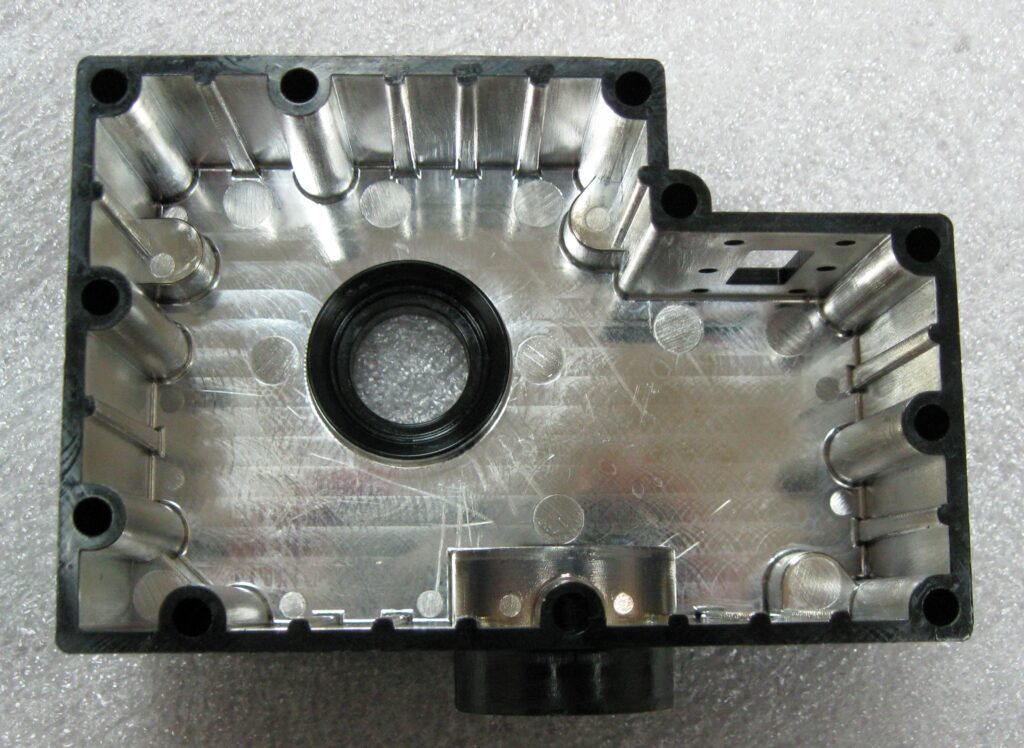
Key Benefits of the Two-Layer Vacuum Metallization Process
1. Superior Shielding Effectiveness
The combination of different metals enhances EMI/RFI attenuation, making the shielding process more efficient across a broad frequency range.
2. Corrosion Resistance
Both nickel and aluminum serve as protective layers for copper, reducing oxidation and extending the lifespan of the shielding material. This makes the metal layers practical for long-term EMI shielding applications.
3. Enhanced Conductivity
By leveraging the high conductivity of copper with the durability of nickel or aluminum, the shielding remains effective even in demanding environments.
4. Cost-Effective Solution
Vacuum metallization is a relatively low-cost process compared to alternative shielding methods like conductive coatings or solid metal enclosures. The ability to deposit precise, thin layers of metal optimizes material use and reduces waste. This is a cost-effective way to achieve EMI shielding.
5. Lightweight and Versatile Especially in applications where weight is a concern, such as aerospace and portable electronics, vacuum metallized coatings provides an excellent balance of shielding performance and reduced mass.
Applications of Vacuum Metallized Shielding
- Consumer Electronics: Smartphones, tablets, and laptops benefit from EMI shielding to maintain signal integrity.
- Medical Devices: Ensures compliance with electromagnetic safety standards for sensitive diagnostic and monitoring equipment. These devices often use vacuum metallization for EMI shielding.
- Automotive Electronics: Protects onboard communication and control systems from interference.
- Aerospace & Defense: Lightweight yet effective shielding is crucial for avionics and military-grade equipment.
- Composites and Plastics: Enables non-metallic materials to achieve a similar level of EMI shielding as traditional metallic components. This expands the versatility of using EMI shielding in various industries.
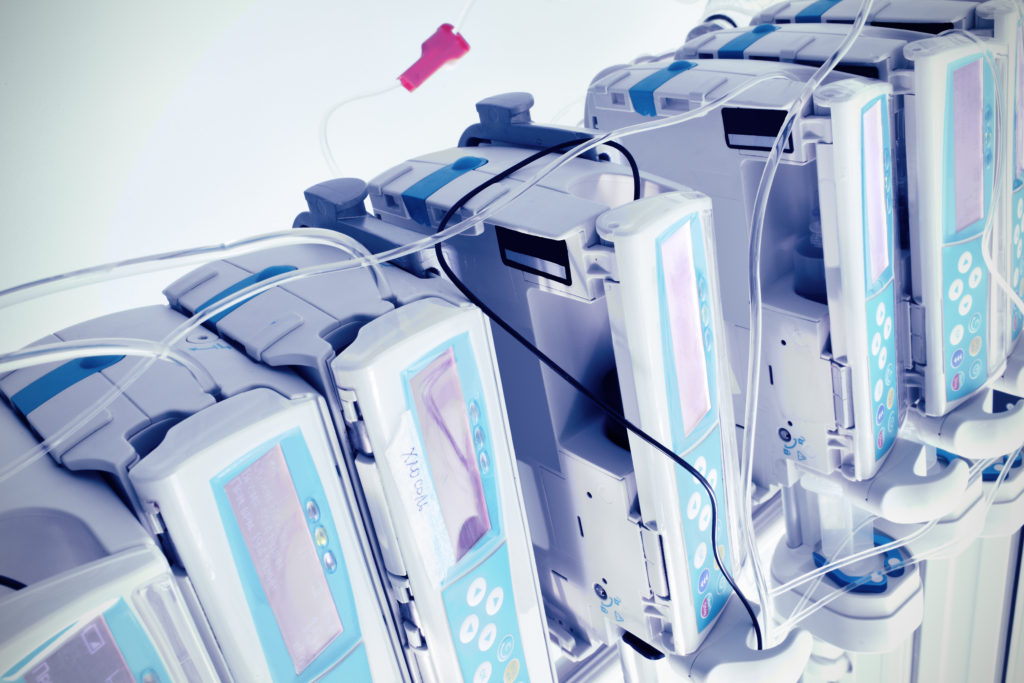
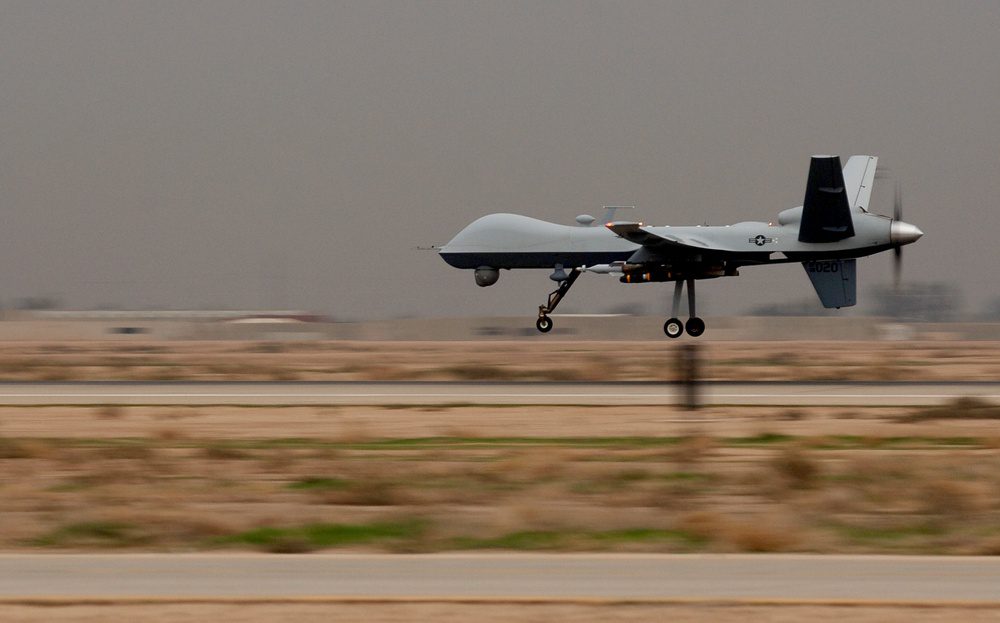
Conclusion
Vacuum metallization is a powerful, cost-effective solution for EMI shielding, particularly when using a two-layer approach. Whether using nickel over copper for its corrosion resistance or aluminum over copper for its lightweight properties, both methods provide superior performance in shielding applications. By applying this technique to plastic, carbon fiber, and other materials, manufacturers can extend shielding capabilities to a broader range of products. As electronic devices continue to evolve, effective EMI shielding techniques like vacuum metallization remain essential for ensuring reliability and efficiency.